Introduction
The primary goal of a safety system is to reduce operational risks and improve the overall safety of a plant over its entire lifecycle. In the event of a demand (out of limit operation) in the process, safety instrumented systems (SIS) are there to ensure that a plant is taken into a safe state, limiting the negative consequences to people, equipment, and the environment.
It is important that organizations in the process industry are able to maintain SIS at optimal level and verify design assumption against actual conditions throughout the plant operating lifecycle. Thus, it is necessary to have the capabilities to continuously monitor and evaluate safety system performance over time. The challenge for many businesses is how to actively manage and maintain their operational safety performance.
During operations, measures need to ensure that safety instrumented functions (SIF) continue to provide the required functionality with respect to its defined safety integrity level. Collecting, documenting and analyzing raw safety data from multiple SIS systems consumes a lot of time and manual overheads. Data needs to be up to date, allowing safety personnel to assess and verify safety system performance against the original design targets. The SIS system performance is likely to degrade as time passes by, which increases the potential exposure to risks.
A customer in China has taken actions to address these concerns by installing Yokogawa’s Exaquantum Safety Function Monitoring (SFM). A software solution from Yokogawa to automatically monitor safety performance for all its SIS systems to reduce the manual work to assess the performance of their safety systems.
SFM automatically collects data from the safety systems and compares actual performance against design specifications. Enabling the customer to easily identify potential risks and have greater visibility on ageing or underperforming safety devices. Providing an efficient means to monitor and analyze SIS systems in order to improve the safety and availability of the plant.
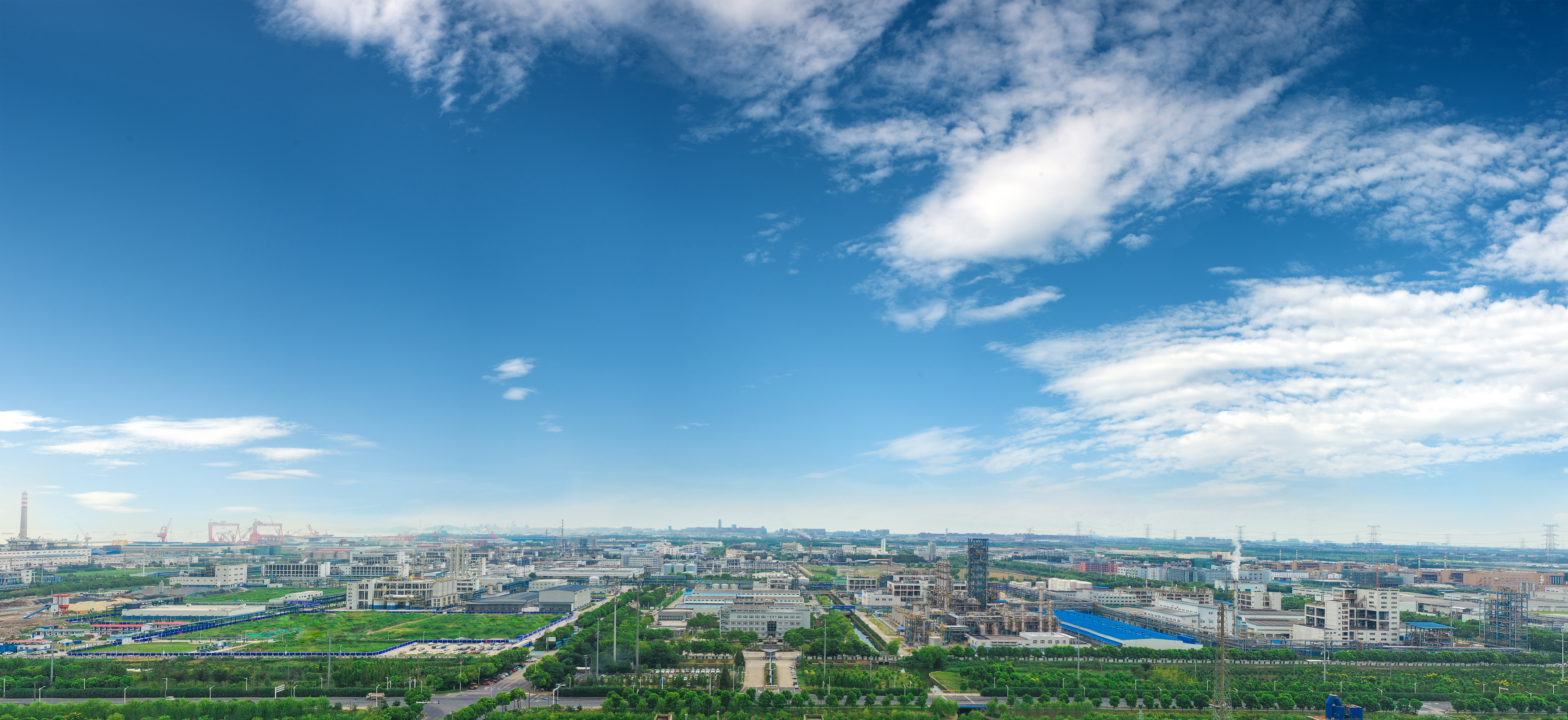
Project Challenges
First SFM project with a non-Yokogawa SIS
In all previous SFM projects, safety data has been collected and monitored from Yokogawa ProSafe-RS safety systems. At this site, most SIS are provided by Yokogawa, with one supplied by a third-party vendor.
The vast majority of control and safety systems is provided by Yokogawa, however one of the Storage Units in Phase I is using a third-party SUPCON system. We faced the challenge of getting safety data from the SUPCON system and making this available to SFM, the first project where SFM has been required to collect data from a non-Yokogawa safety system.
.png)
Two Months to Deliver the System
This project included some very specific targets and deadlines for system delivery. One competitor provided a very low bidding price and assured the customer that they could meet the project specifications and timescales. There were doubts and reservations from the customer relating the proposal and whether they could satisfy the delivery schedule.
Yokogawa’s sales team worked very closely with the customer to fully understand and appreciate the requirements relating to the project, particularly in reference to the two-month system delivery timescales. Yokogawa’s previous experience and knowledge of other SFM projects was clearly demonstrated, removing any doubts or hesitations from the customer and helped secure this project.
First deployment in China
SFM has been deployed in various sites and locations to monitor safety system performance for customers globally, but this is the first time SFM has been deployed in China. There were many challenges associated with all project phases from early sales activities and discussions, right through to project implementation and training. These challenges were easily overcome with a collaborative effort from many Yokogawa colleagues in China, Singapore, Japan and the United Kingdom working together to secure this project.
Meeting the Project Scope
There were a number of key requirements in the scope of work for this project which are shown below:
Monitoring and analysis of safety performance data of 151 SIFs across thirteen control and safety systems (12 Yokogawa and 1 SUPCON) in Phase I and Phase II of the plant
A set of capable analysis tools will be provided to identify safety functions and the differences between expected design and actual operations
More than 600 (593 DCS + 58 ESD, SIL 0) DCS interlocks need to be implemented and monitored
Safety performance data will be available online for users in the office
SFM is able to monitor and display SIF safety performance data from all safety systems via OPC. Through the automated collection of safety data, users are able to compare this information against assumptions made in the design specifications to help identify potential risks and easily detect aging or deteriorating safety devices.
Valve deterioration can occur in safety devices including “Chopper valves”, special on/off valves or override solenoids which are used to force the normal control valve into a shutdown state. These are the Final Elements of a SIF which must act within a designed time and fulfil its intended protective function alongside sensors and logic solvers. During the operations phase, SFM is monitoring and recording the durations of final element transitions and valve travel times that can be assessed against the ‘designed-in’ performance targets as described in the SRS.
In addition, SFM is configured to monitor over 600 DCS interlocks alongside the 151 SIFs. To help differentiate between Interlock triggers and SIF actuations, all interlocks are configured as safety integrity level of zero (SIL 0) in this SFM installation.
Users can easily access the safety performance dashboards and reports via the SFM web user interface, which is available to users outside of the control room. Office personnel will be able to access consistent, reliable, and accurate safety performance data that is collected automatically to save time and resources.
Key Takeaways
First SFM Project on a third-party SIS
This is the first SFM project requiring SFM to collect and monitor safety data from a non-Yokogawa safety system. In this plant, twelve out of the thirteen control and safety systems are Yokogawa, the other is a SUPCON system.
This project validates the use of SFM in projects involving non-Yokogawa safety systems. SFM has the capability to access safety data from third-party safety systems that support an OPC interface.
%20large.jpg)
Reduce manual effort to monitor SIS performance
One of the main objectives was to reduce the amount of manual and labor-intensive work to gather, process and evaluate safety data. They wanted the means to drastically save time and increase the accuracy of collecting safety data from multiple safety systems and free-up this valuable resource.
With the installation of SFM, this critical safety data is collected automatically and presented in a user-friendly format via a web user interface. Users are able to easily access safety data and reports which are readily available and error free and minimizes the manual work for safety experts. As an example, the processing time for a quarterly safety evaluation has gone from one-month to just two-days, representing a huge saving in terms of time and resources.
Tight Delivery Timeframe
The customer had a very ambitious two-month installation schedule that was crucial in winning this project. Yokogawa colleagues worked closely with the customer to understand the requirements of this project. There was another company that put forward a proposal, but the customer doubted they could meet the specifications and delivery schedule.
Yokogawa on the other hand has the relevant capabilities, experience and knowledge in safety applications and were able to deliver the schedule on time. This combination of factors was enough to convince the customer to award the project to Yokogawa.
First SFM project in China
SFM has been successfully deployed on a number of projects around the globe, with the goal to adopt the best safety practices and adhere to global standards like IEC 61511 Edition 2, COMAH (Seveso III) and OSHA. This project is the first to be installed in China proving Yokogawa’s ability to deliver world-wide and opens the opportunity for further deployments in this region.
With Yokogawa safety engineers, sales teams and product support coming together from different offices and regions working alongside the customer, we successfully delivered this SFM project.