A leading LNG project, maximizes efficiency with Exaquantum/SFM, significantly reducing man-hours to compile safety reports while enhancing data collection and monitoring for high volume of SIFs.
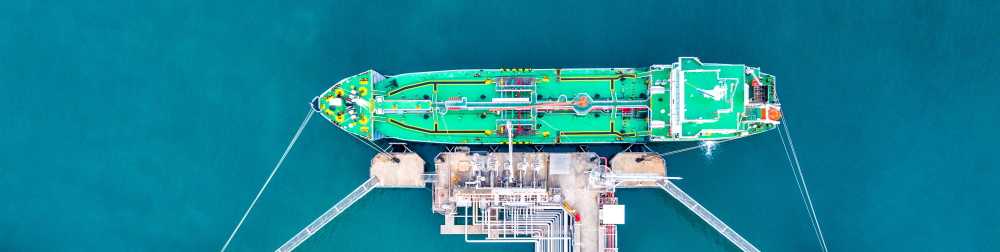
Summary/Outline
Monitoring functional safety is a crucial practice that yields valuable data and insights regarding the performance of safety-related systems. Through careful analysis of collected safety data, organizations can identify areas for improvement, optimize safety functions, and enhance the overall reliability of their systems.
However, the process of verifying safety data can be labor-intensive. It consumes significant manpower to track safety events, monitor and record activations of safety instrumented functions (SIFs), and compare performance over time. The production and interpretation of safety reports also require considerable time and effort. Unfortunately, manual procedures like these are prone to errors and inaccuracies.
To address these challenges at one of the world's largest LNG projects, a customer sought a software solution to support their plant safety management practices. They aimed to monitor their entire CENTUM VP and ProSafe-RS control and safety system and streamline the generation of safety reports in an efficient and cost-effective manner. Their objective was to reduce the number of man-hours required to collect and monitor SIF performance data and compile safety reports.
Yokogawa’s Exaquantum Safety Function Monitoring (SFM) solution emerged as the ideal choice. SFM offers automated collection, processing, and presentation of safety data from their control and safety systems, enabling effective monitoring and analysis of key safety key performance indicators (KPIs). By accessing comprehensive safety performance data, users can promptly identify safety issues, minimize maintenance activities and enhance safety designs.
To ensure SFM's suitability in meeting these specifications, a six-month trial was conducted. During this trial period, certain areas were identified where SFM did not entirely fulfill the operation need. Consequently, Yokogawa incorporated enhancements based on the feedback, addressing the identified areas, and the latest release of SFM (R3.40.10) now incorporates these improvements.
Project Background
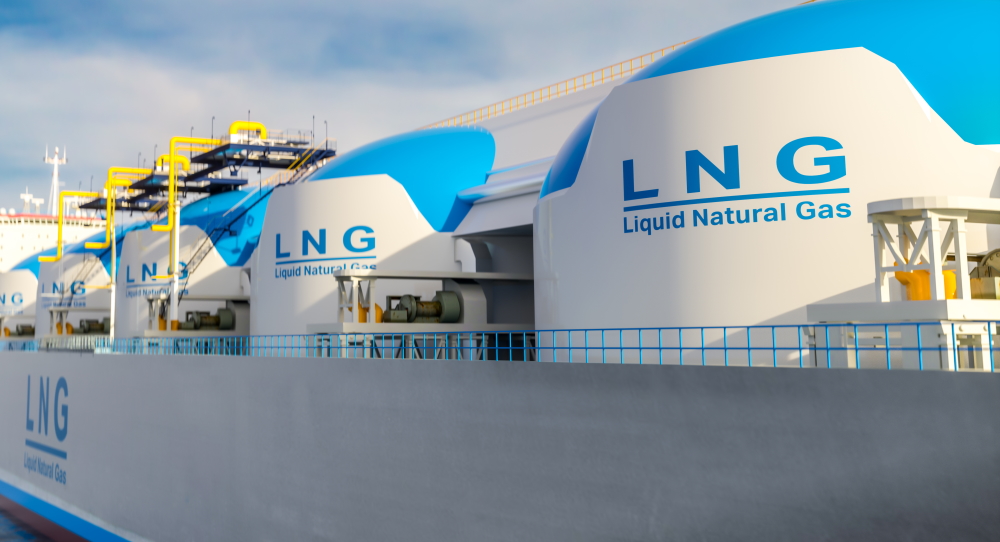
Yokogawa holds the distinction of being the original supplier of the CENTUM control system and ProSafe-RS safety system at this site. It stands as one of the largest liquefied natural gas (LNG) projects worldwide. Encompassing a three-train LNG facility capable of producing double digit million tonnes per annum, along with a domestic gas plant that can supply gas to the local area. Given the substantial scale and strategic significance, the project will continue to play a vital role in the national economy for many decades. By meeting the global demand for cleaner-burning fuel, it serves as a cornerstone in the quest for sustainable energy solutions.
Trial Installation of SFM
To evaluate the capability of Yokogawa's SFM solution in meeting the customer’s specific safety requirements, a trial installation of SFM was implemented on a virtualized environment. This approach offered the flexibility to adapt to the resource demands of the SFM system, ensuring optimal performance.
A mutually agreed upon six-month trial period was established, providing ample time for the customer to ascertain whether SFM could effectively support their plant safety management practices, monitor the entirety of the CENTUM VP and ProSafe-RS systems, and streamline the generation of safety reports.
During the trial, SFM was configured to monitor an extensive set (over 1,000) SIFs from the LNG/AGRU Trains. This large number of SIFs was crucial in providing an accurate representation of how SFM would meet the project requirements. The focus was not only on monitoring and assessing safety data but also on examining how SFM would handle and process such a substantial volume of SIFs. In the final SFM deployment, the monitoring scope would be expanded to include the inlet and other utilities, resulting in a total of several thousand monitored SIFs.
Outcomes from the Trial Installation of SFM
SFM is being utilized to monitor SIF demands (activations) and valve actuations. Throughout the trial period, several aspects of SFM were identified that required alignment with the customer's specific requirements. While SFM already possesses the capability to monitor and record SIF activation data, the existing method did not align with the customer's preferred format for recording and presenting the information. As a result, enhancements were necessary to ensure that SFM accurately captured and presented the data in a manner that met the customer's expectations.
SIF ActivationsBefore we take a look at the changes needed, let us first define what a SIF is. A SIF is a safety measure that senses a potentially hazardous condition and automatically performs an action to return the process to a safe condition. A SIF is implemented as a functional combination of one or more sensors, a logic solver and one or more final elements.
Exclude SIF Activations that do not have Final Element actuationsThe customer wanted the capability to exclude SIF activations that do not have Final Element actuations in their safety reports. This can happen in situations where multiple SIFs have the same Final Element. In SFM the first up SIF will only have the associated Final Element actuation.
Exclude SIF Activations during maintenance activitiesThe customer wanted the capability to filter out any SIF activations during maintenance activity, or in maintenance override (MO) as this is not a safety event. For example, proof test or faulty devices waiting for replacement are not a demand (Trip Event). They required SFM to record the SIF activation, but with an option to filter out these events from the web page display.
Associate Final Element actuation with overall SIF Response TimeThe customer wanted the Final Element actuation to be associated with the overall SIF response time. In some situations, Final Element actuations can be delayed either through logic controller or the delay in signal to actuate the Final Element. With such a delay, the Final Element is not associated with the SIF activation.
Additional Information Associated to Final Elements
The customer wanted to have additional details associated to the Final Element shown on the webpage to enhance the information available, including;
SIF Activations in Specific Report FormatThere was an expressed need for a comprehensive report that presents SIF activations and their corresponding Final Element actuations in chronological order, organized by date and time. They specifically requested filters to facilitate identification of specific timeframes or plant areas. The objective was to enable users to easily comprehend plant trip conditions, and the report should be available for printing or publishing. By providing a clear analysis of SIF activations alongside associated Final Element actuations, the report serves as a valuable tool for validating the effectiveness and reliability of SIFs.
SFM Enhancements in R3.40.10
Exclude SIF Activations that do not have Final Element actuations
SFM now has an additional filter ‘Exclude No Actuation’ which has been added to the SIF Activations web page. This new filter option allows SIF Activations with no associated Final Element actuations to be excluded from the SIF Activations web page display.
Exclude SIF Activations during maintenance activities
SFM now has an ‘Exclude Active Maintenance Override' filter which has been added to the SIF Activations web page. This allows users to filter out SIF activations that occur when the SIF is in Maintenance Override (MO).
Associate Final Element actuation with overall SIF Response Time
SFM processing that associates the SIF activation to the Final Element actuation has been changed. SFM now uses the SIF Activation + Overall SIF Response Time or a default period if the Overall SIF Response Time is not defined. Users will have the ability to configure and define the Final Element actuation within SFM. With the SIF response time now being configurable, the association of the Final Element actuation to the SIF Activation using the SIF response time as the association period, would enable a possible delay between the SIF activation and the Final Element Actuation.
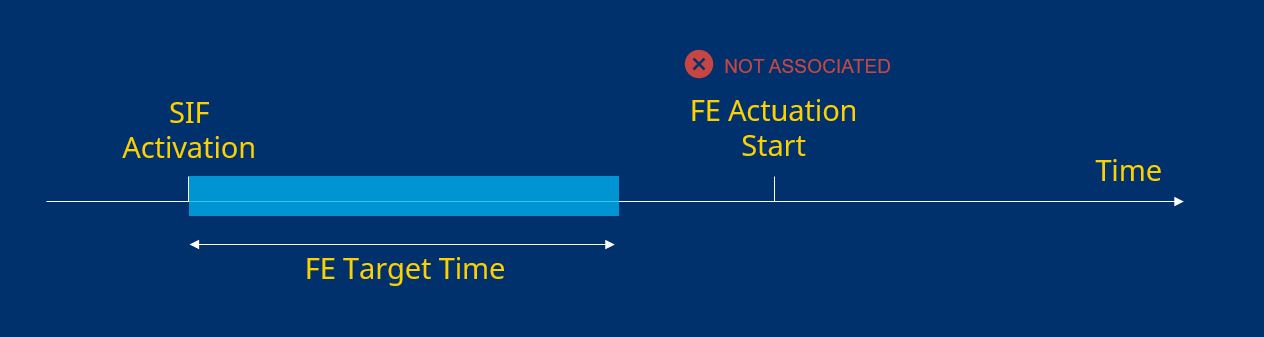
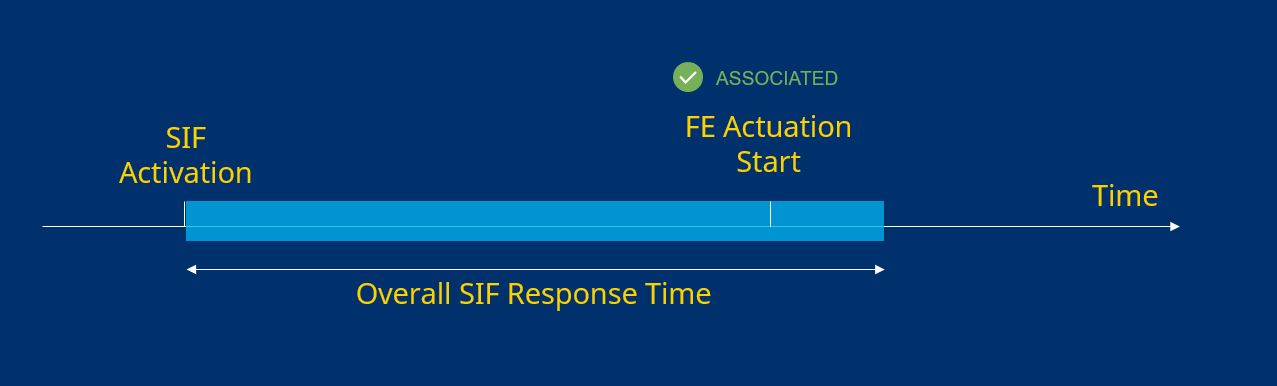
Additional Information Associated to Final Elements
SFM now allows for additional information to be associated to Final Elements in the SFM configuration file to be displayed in the SIF Activation Detail web page when the mouse pointer hovers over the final element. The type of information displayed is defined by the user’s requirements.
SIF Activations in Specific Format
SFM now provides an additional Trip Investigation Report. This new report displays a list of SIF Activations and associated Final Elements ordered in chronological date/time order to aid investigations.
Tangible Benefits
The customer achieves substantial time savings on an annual basis through the implementation of SFM, which enables efficient collection, monitoring, and recording of SIF performance data. By leveraging SFM, the organization eliminates the need for labor-intensive manual tasks such as looking up SOE (Sequence of Events) data, as this information is readily accessible through SFM reports or displayed on the web page. Previously time-consuming activities that required several hours to complete can now be accomplished within minutes, leading to significant efficiency enhancements in report generation and investigative processes:
- Trip investigation reporting efficiency is improved by 75%~92%
- Independent Protection Layer reporting efficiency improve by 75%~83%
- Final elements investigation efficiency improved by 83%~92%
In addition, they have the ability to quickly verify the health of the SIF and promptly restart the plant is instrumental in minimizing the loss of opportunity cost. By swiftly responding to a demand, the customer can respond promptly, reducing the duration and the potential negative impacts of plant downtimes and increasing overall plant availability.