The Problem with Nuisance Alarms 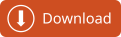
%20cropped.jpg)
A well-managed alarm system can reduce risks and enhance the safety of plant operations. The alarm system is often the first line of defence that helps avoid serious process incidents - an indispensable component of process control that attracts the attention of process operators to any abnormal conditions in the plant. However, in practice, many process plants suffer from poor alarm system configuration which leads to nuisance alarms and alarm floods. These compromise safety and inhibit the effectiveness of process operations, due to operators missing important alarms. This is a problem for organizations who struggle with operational clarity and consistent performance in their day-to-day operations.
Alarm systems that have not received the appropriate attention and resources, or have been poorly configured, often encounter the issue of nuisance alarm. These are alarms which are triggered when either no abnormal condition exists, or when no operator action is required. Such alarms are given little or zero credibility by the operators and are often ignored or disconnected. This can lead to doubts about other alarms in the system, reduce the confidence of operators in the alarm information, and potentially distract them from important alarms. To improve this situation, competent individuals and subject matter experts review every alarm in the system, organized in terms of priority, so that the important work is tackled first.
A large petrochemical producer in Asia wanted to monitor alarm system performance with the ultimate goal of reducing their alarm count and minimizing the distraction of nuisance alarms with better plant data visualization. They are the largest producer of Phthalic Anhydride in the region. Phthalic Anhydride (PAN) is used in industries such as flexible PVC, plastics, paints, construction, transportation and marine. They wanted to segregate their plant data and alarms and events for their two plant processes, Maleic Anhydride (MA) and PA Phthalic Anhydride.
To facilitate performance gains, they identified some key performance indicators on their alarm system. This required access to data and autonomous reporting capabilities for their alarms and event data that could be easily shared and distributed, providing an overview of alarm performance for the senior management team. As with many process plants, they required streamlined access to these KPIs and reports, accessible on desktop and portable tablet devices on the business domain that allowed for quick and convenient access to system data to display layout of process.
By closely monitoring alarm system data and taking actions to resolve concerns, it will help the business deliver superior quality products and expand the production capabilities to stay ahead in a highly competitive industry.
Solution
A healthy alarm system provides operational transparency that optimizes day-to-day operations and provides a solid foundation for more consistent performance and expanded production capabilities. Yokogawa was approached by the customer to identify solutions to help monitor the alarm system performance and pinpoint areas of concern that were specific to their process requirements.
With Exaquantum, Yokogawa’s Plant Information Management System provides a flexible and adaptable solution that collects important process values which can be stored and monitored over time. It also provides the investigative capabilities to assess alarm system performance with the Alarm Reporting and Analysis application (Exaquantum/ ARA). This versatile solution allows the customer to select and combine the respective reports from the plant information system as well as the alarm reporting system, whichever is most appropriate for their requirements. The alarm and reporting package includes a number of KPI reports that are generated on the production system that conform to alarm industry standards (EEMUA 191 Edition 3, ISA 18.2 2016, IEC 62682).
Eleven reports have been identified to help reduce the alarm count and lower the number of nuisance alarms that are presented to the operators. This approach enables the customer to use performance measures to identify nuisance alarms which occur most frequently and are most likely to trip and gradually work through these systematically and take the necessary corrective actions.
With an intuitive and user-friendly web user interface, data, mimics and automatic reports are seamlessly produced for their KPIs on their alarm system, providing enhanced visualization on iPads and desktop devices on the business network. To streamline data access and communication, the solution generates reports automatically that can be used by senior management wherever there is an internet connection.
Deployed on an existing Yokogawa distributed control system on site, the integration and configuration was straightforward with minimal issues that was completed in phases. This allowed for Tag lists extracted from the CENTUM VP engineering workstation databases to be directly imported and configured for the alarm reporting package (Exaquantum/ARA).
Key Takeaways
Reduction in the number of alarms
Comprehensive reports produced by the alarm reporting package enabled the customer to identify and systematically work through frequent nuisance alarms in order to reduce the number of alarms presented to operators by 80%. By significantly reducing the number of alarms, it can lesson operator stress and allows more time to consider and address more important alarms which may have been previously overlooked.
Enhanced data visualization
Exaquantum is a plant information management system that collects, stores and processes process data and alarm and events data simultaneously. By utilizing in excess of 100 web graphics and eleven alarm analysis reports, this user-friendly application allows operators to design and combine relevant reports to fulfil their requirements, highlighting key KPIs with live and historic data. Having this information readily available provides operators with the tools to quickly spot issues and take the corrective actions to achieve operational consistency.
Data on the go for senior management to take decisions
The needs and requirements for senior managers of process plants are constantly changing and they need access unrestricted access to key operational information anytime and anywhere, supported by portable devices and tablets. Exaquantum’s web user interface provides support for tablet devices and iPads that enabled the senior management team to access information regardless of their location. With more freedom and flexibility to access plant data with improved visualization of important process information and KPIs to enable a more streamlined approach to production management. Senior managers are now notified and informed if any changes to performance occur, allowing them to take the corrective actions to maintain swift and efficient operations.