Use of Live Data 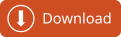
Recommended good practice for subsea production systems require sensors to be installed that measure pressure safety high (PSH), to provide over-pressure protection on downstream vessels in a production train. Similarly, pressure safety low (PSL) sensors are required to provide under-pressure protection. These pressure safety devices must use live input data to determine the safety high and safety low values to help prevent over or under pressurization of a vessel if they are to adhere to regulatory requirements.
The Bureau of Ocean Energy Management Regulation & Enforcement (BOEMRE) require Gulf of Mexico operations to use range charts to determine the safety settings of PSH and PSL for pressure safety devices. Range charts (previously referred to as Minerals Management Service Trends) display a set of data points that require two values per data point. These values consist of a high value (PSH) and a low value (PSL) that defines the range for each data point. Having access to this live pressure data will provide information on the current pressurization of a vessel; but how do you collect and store all these data points and can you record these values accurately that satisfy regulatory requirements. Are operators confident that they really know the highest and lowest pressures over a specific time period. This requires a repeatable process that can calculate range values for a defined date/time that is easily accessible from the control room.
Organizations that operate in these environments can benefit from an effective method of collecting and storing all settings for all sensors that is maintainable and repeatable over time to help prevent over/under pressurization of their pressure safety devices.
Solution
Yokogawa provides an effective solution to access live data to determine the safety settings for pressure safety devices. Exaquantum collects and stores pressure data and via its AutoTrend software application, it provides a range chart with the ability to display real-time and historical trend information for PSH and PSL values. The range chart tracks and monitors pressure safety devices that can be printed or saved electronically over a selectable time period. The PSH and PSL values are calculated based on the latest data and time range applied. If the date/time range is changed, the PSH and PSL values are updated and re-calculated based on this new information, conforming to recommended best practices and BOEMRE standards relating to pressure sensors installed on subsea production systems.
To improve operator efficiency, navigation to the range chart is easy accessible from the HMI screens in the control room. Users can easily see which sensors to track and select which tags they want to chart with simple drag/drop functionality. An in-built calculation engine helps to determine the safety high and safety low values for pressure sensors with a quick and efficient range chart solution. In addition, every pressure device that is charted can be quality checked with a pass/fail quality check.
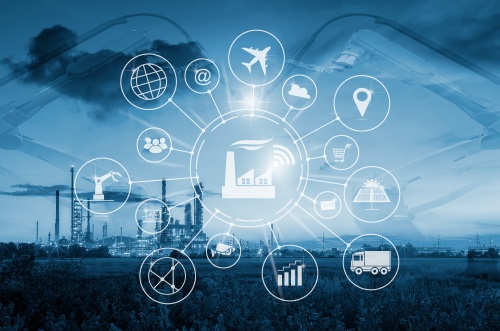
Key Takeaways
Uses live data to easily determine the safety settings for pressure safety devices
This software solution provides control room operators with an easy and intuitive tool to monitor and track pressure safety devices that uses real-time and historical trend information. The range chart provides the PSH and PSL values for selected devices via a simple drag and drop menu screen over a defined period of time that can be printed or saved electronically as needed.
Regulatory Compliance
The BOEMRE standards and recommended practice regarding pressure sensors state that safety settings of PSH and PSL are required to use live input data. This Range Chart software meets these requirements and provides the necessary evidence to support regulatory compliance.
Sustainable Process
Organizations that operate in the subsea production systems environment require an effective method of collecting and storing all settings for all sensors to help prevent over/under pressurization of their pressure safety devices. As part of an ongoing requirement, it is important that pressure safety data is maintainable and repeatable over time.